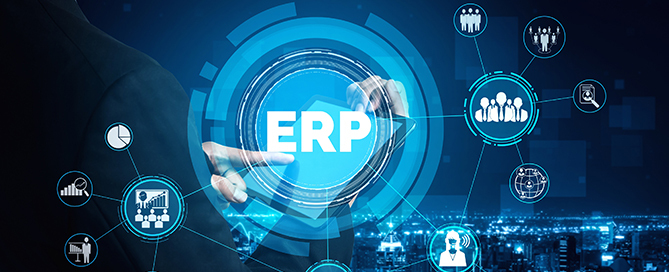
Have you been considering an ERP implementation to optimize operations in your manufacturing enterprise? Data collected over the years on ERP implementations reveal that 50% fail the first time around. There are many reasons why this may happen which is all the more reason to get your implementation right from the get-go. Despite these odds 49% of enterprises who did manage to successfully implement an ERP system reported a significant overall improvement in business processes.
In this blog we’ll cover some of the best tips and guidelines for documenting busines processes, how in depth it should be and how to make use of this documentation while selecting your ERP. Good documentation serves to help you figure out what is critical in the new ERP system and what is non-essential.
Why Do You Need ERP Process Documentation?
You could consider an ERP process documentation a sort of instrument that can help highlight your ERP needs so that you can select the vendor who can meet your expectations. Furthermore, details that you gather during this time play a huge part in steering your implementation. This stage in essence is designed to better define the objectives of the implementation while simultaneously eliminating vestigial processes.
Process documentation can also act as a sort of refresher for employees on the workings and know-how surrounding end-to-end workflows. Chances are they may even be able to pinpoint process flow weak spots that can warrant process improvement brainstorming ultimately geared towards standardization. Plus, getting the work force involved inevitably leads to increased inter-departmental communication. This can make individuals in one branch make decisions more diligently bearing in mind the impact it may have on their counterparts.
Having thorough documentation in place with goals and targets can be a good source to refer to during the course of the ERP implementation, particularly the early stages. In this way you can make sure that all activities are geared towards an effective and successful implementation.
Recommendations for ERP Process Documentation
- Consolidate ERP Needs
Summarizing the ERP needs is an important aspect of process documentation. While the entire documentation may be detailed and lengthy having an outline of the core requirements for your ERP implementation can come in handy. While putting this list together focusing of high-level capabilities like CRM functionality should be highlighted. In addition to this if there are certain elements that crucial in order to benefit from their value addition, they can be explained further in the documentation.
2. Begin with Primary Processes
Order procurement and fulfilment are two core processes that you can begin your process documentation with. These workflows can be laid out at a high level, narrowing down on the needs of downstream employees and tracing how it reaches them.
3. Implementation Templates
This includes all the stages and steps of the implementation. This is useful in the future for employees to understand how the implementation was undertaken. They can also find this guideline effective if there are any upgrades that the company would benefit from in the future.
4. Clarifying the Root Cause
When reflecting upon your existing business processes you may find yourself frequently wondering why certain workflows have been kept as they are. Tasks might be conducted simply based on the reason that they always have been. When you really consider the root cause behind a certain action it can make way for a better understanding of whether or not a process is required or instead if it can be improved.
Processes can be streamlined and regulated for a leaner, more efficient system. This is a factor that ERP consultants like to focus on as opposed to ERP vendors who are simple happy to provide.
5. Standardize Workflows Allowing A Degree of Flexibility
When you have an enterprise that is located across the globe it is all the more important to have a consistent process that allows for flexibility. Even though standardized workflows can allow for improved operational efficiency, it is crucial to leave some room for adaptations that may come along in the future.
A magnifying glass is needed when deciding on standardization procedures since at first glance they may appear consistent but upon further inspection can reveal that not all the details are the same across all locations. Take for example the pulling process, it might not be followed throughout the warehouses on all locations due the obvious differences in layout. Undertaking a thorough process documentation can make such constraints on standardization more apparent.
6. Maintain High-Level System Upgrades
Part of the documentation entails listing what process improvements your ERP implementation needs to make available. The best course of action is to remain within the confines of high-level system improvements. Going in to too much detail during this phase can lead you to over-modify your chosen ERP system in order to fit the requirements you have listed out in your ERP process document.
7. Have Every Team Involved
An ERP system’s sole purpose is to make life easier for everyone involved in the workings of the enterprise. As such they should be given an opportunity to voice pain points and other such complaints that they have identified whilst working within the existing outlined process guidelines. Their input can be valuable since it may comprise of overlooked issues. To have a better understanding of their suggestions you could categorize them into the following sub-sets:
- Process-based
- Systems-oriented
- People-focused
Are you interested in a new ERP implementation for your enterprise? Would you like help documenting your ERP process? Our team at SolutionsX would be happy to help. We provide expert solutions for your organization’s ERP needs. With more than a decade of manufacturing industry experience our SolutionsX consultants are not only a point of contact but an ongoing personal guide in building and integrating a system that fits with your operations, goals and culture. Reach out to us at SolutionsX to find out more.